Repairs
Clicks, squeaks, buzzes, rattles, broken strings and sticking or dead keys will inhibit your playing experience and overall enjoyment of your piano. Pianos are intricate devices with approximately 9,000 individual parts in the action, 220 strings, as well as a number of parts that make up the damper and pedal systems, bench, and case.
Keeping your piano in good working order makes it enjoyable for all who play and listen, and is especially important for a young beginner’s chance for success when learning to play.
David Brisson, RPT, has extensive experience repairing pianos in homes, schools, universities, and churches.
Repair and maintenance recommendations are included as part of a standard tuning service. However, if you are uncertain if your piano is serviceable - perhaps the piano has several dead keys that do not play or make any sound at all or there are multiple broken strings - it is best to schedule a Repair Estimate Appointment.
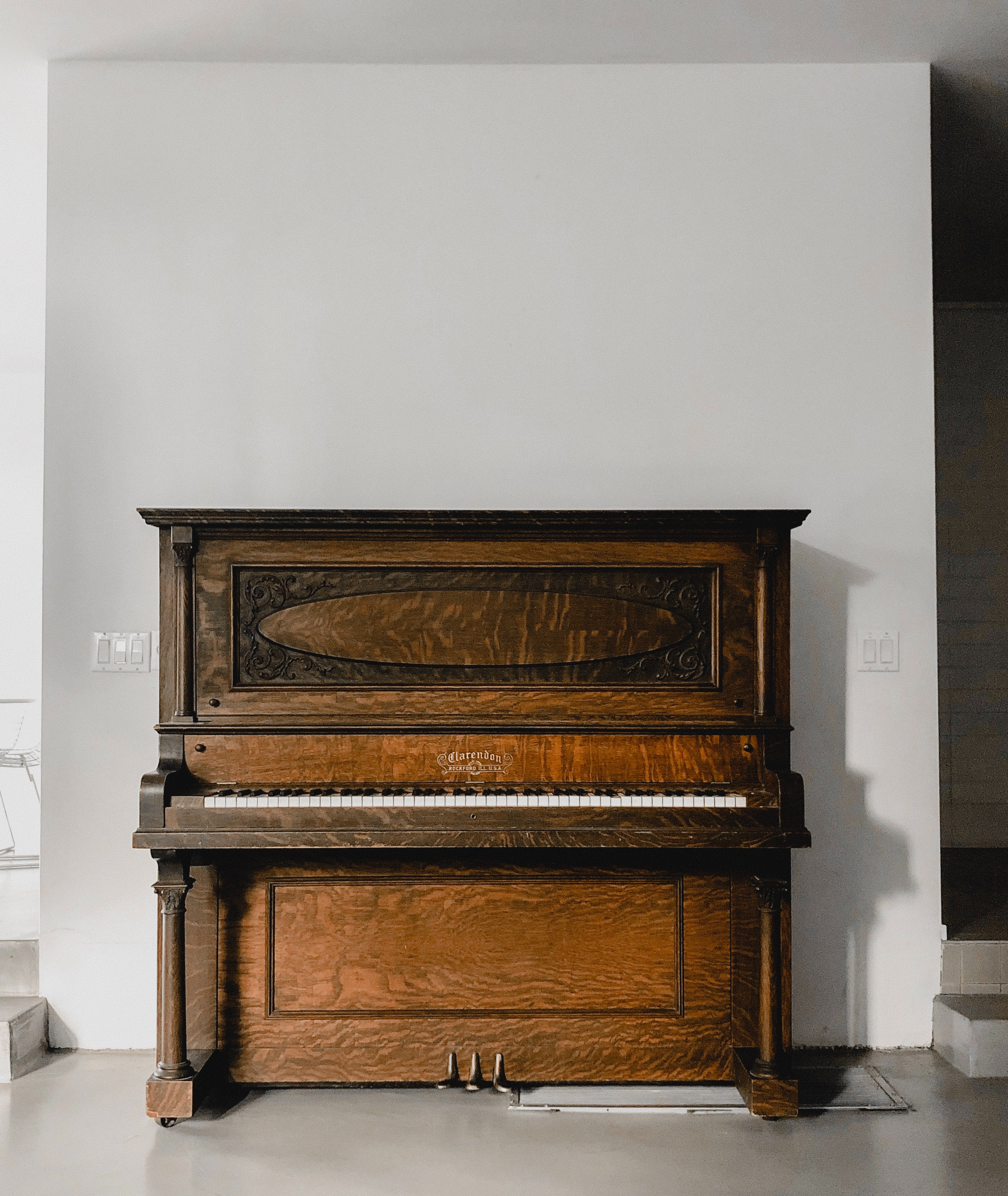
Appointment Info and Fees
Repair Estimate $125- It takes about an hour for a thorough examination of the piano and review of the estimate with the customer.
- The $125 fee will be applied towards the cost of any repairs made.
- Repair estimates are good for a period of 90 days.
- Together, we will determine the best course of action for your piano.
Frequently Asked Questions
This decision depends on the age, make, model, overall condition, sentimental attachment, the intended use, and pre/post-repair valuation of your piano. When the costs of repairs and/or restorations far exceed the value of the instrument, it is advised that a replacement instrument be considered as a better alternative than investing in the current piano.
Both terms refer to restoration work, and partial or full ranges apply.
Rebuilding as defined by the Piano Technicians Guild:
“A used piano that has been disassembled, inspected, and repaired as necessary with replacement of all worn or deteriorated parts, re-assembled, tested, and approved to at least the same tolerances as a new piano of like manufacture.”
Reconditioning as defined by the Piano Technicians Guild:
“A used piano that has been put back in good condition by cleaning, repairing and adjusting for maximum performance with replacement parts where specifically indicated.”
Piano strings are made from steel music wire. When the wire is stretched beyond its limit, it becomes so weakened it can no longer bear the force of playing or tuning; thus it will break.
Aside from strings stretching, oxidation, rust, and impact stress are leading causes of string deterioration.
Properly shaped hammers help prevent broken strings. Deep string cuts in badly worn hammer surfaces is the main cause of impact stress leading to broken strings. Deep string cuts contact the string with a flatter and larger surface area than does a well shaped rounded hammer. Frequent heavy playing on performance and practice pianos in institutional settings, especially where lots of power is constantly demanded in loud environments, are much more prone to broken strings than the average use of a piano in a home setting.
There are a variety of reasons a “sticking” key can happen. Tight key bushings are the most common, followed by too tight of a fit at the balance rail hole in the bottom of the key. Other possibilities include foreign objects that have fallen in between two keys, such as a coin or pencil lead, or the key binds against a tight case part, such as the front keyslip, the key upstop rail, or one of the cheek blocks.
There are ideal ranges of friction for all of the moving parts of the actions, and how they operate as a whole is referred to as “touchweight.” A piano with high friction can feel sluggish and heavy even to the point of being completely frozen or locked up. Too low of friction can cause the parts to malfunction and the pianist will feel like they do not have control while playing. The loose parts will not travel in straight paths, will make clicking noises, and can lead to broken parts and more costly repairs.
A friction reduction is the process of lowering friction in the keys and the action to dramatically reduce touchweight and improve the feel of the keyboard and tone of the piano.
The process is as follows: The action is properly weighed off to measure touchweight and friction. Friction can be addressed in both the keys/keyframe and the top stack of the action. In the key, the balance rail hole is properly sized and reamed, the key bushing felt is sized, ironed, and treated with a Teflon powder to reduce friction. Key pins and capstans are then polished and lubricated. In the top stack of the action, friction is corrected at all action centers, either by reaming and repinning, or by use of a lubrication or sizing solution. The knuckles and whippen heel cushion are also treated with Teflon powder. The action is then reassembled and measured for touchweight and friction.